Modernizing equipment feedback loops
Summary
Providing better-fitting gear to underrepresented aircrew, such as female pilots, is one of the U.S. Air Force’s (USAF) top priorities. Their Human Systems Division (HSD) engaged us to modernize the processes and technologies that allow aircrew to get the equipment they need to perform their best.
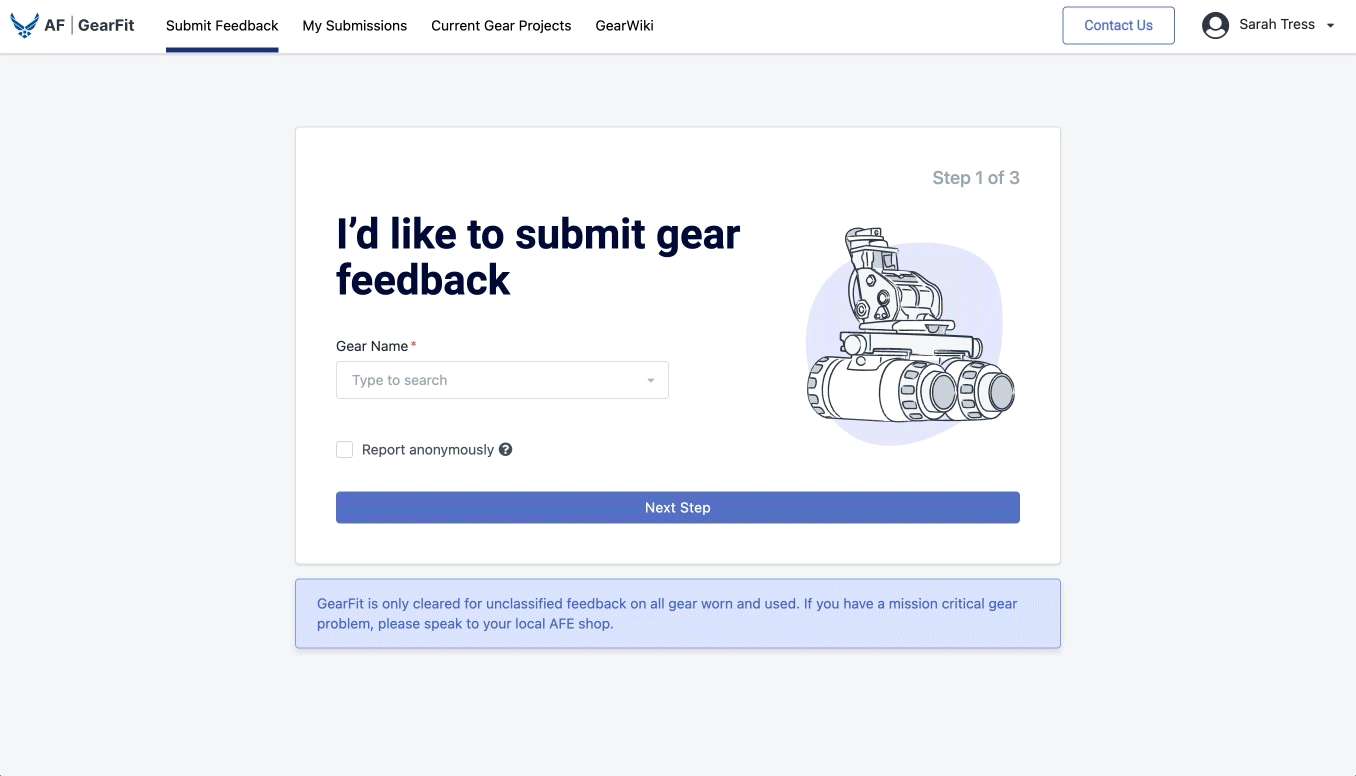
The challenge
Organizations in the defense, security, safety, and healthcare fields often lack the data and systems to meet the complex equipment needs of their diverse workforce. This can result in critical issues that compromise job performance and safety. For the U.S. Air Force’s Human Systems Division, solving this problem is a top priority that goes all the way up to the Secretary, and even Congress.
In certain situations, having ill-fitting gear, such as harnesses and survival vests, can result in a loss of life. If an aircrew member ejects from the aircraft with equipment that doesn’t fit, they can be severely injured or lose their life.
Captain Lauren Ellis, U.S. Air Force
To address this challenge, HSD engaged us to build a digital platform called GearFit. In 2020, we launched a minimum viable product (MVP) to gather gear-fitment feedback from aircrew, initially targeted at female pilots. After we relaunched on an Air Force-wide platform in 2022 and marketed it through channels such as the AF Portal, the platform received a spike in submissions. As a growing population of aircrew have used GearFit, we’ve shifted our focus to address the systems around equipment feedback.
Historically, the USAF hasn’t had a defined method for gathering, routing, and responding to gear fitment issues. As a result, HSD has been unable to consolidate and analyze feedback, which has hampered their ability to make improvements. For aircrew, learning and communicating about equipment is also difficult. Aircrew often don’t have time to find the name of gear, let alone provide feedback about it. In addition, many avoid seeking help because of the “tough-it-out” culture of the military.
To enable the USAF to successfully gather feedback about gear and respond by providing safe, suitable gear, we set out to tackle these challenges:
- Flow of information: To make an impact, data submitted to GearFit needs to reach the people in the USAF who can enact the appropriate long-term changes. When proper gear is available, information about it must reach the aircrew who needs it.
- Staffing: HSD needs real people to manage and respond to gear feedback, but has limited staffing and funding.
- Data analysis: To take informed action, HSD and other decision-makers need a way to view data holistically and find trends.
The solution
To solve the USAF’s equipment problems at scale, Skylight has continued to make GearFit as fast, simple, and psychologically safe to use as possible, while exploring improvements beyond the platform. The result is a system of solutions, both technological and operational.
To begin we first realigned with our HSD stakeholders on goals and strategy. This expanded on the service design activities we conducted at the start of the project, which gave us and HSD a more holistic understanding of the problem space and targeted opportunities for improvement. We emerged from the realignment conversations with an understanding that many in the Air Force beyond one program office have a stake in gear issues and management.
Next, we embarked on a research effort to identify the key players beyond HSD with an interest in the data GearFit provided. This research prompted an experiment with Data Reports, quarterly summaries of GearFit data that we distribute to a wide range of stakeholders. Follow-up interviews with these stakeholders proved that the reports were valuable and are informing which metrics to prioritize in GearFit moving forward.
To address gaps in staffing, we’ve developed new GearFit features, as well as processes, to support HSD. As we work with the Air Force to create a long-term staffing solution, we’ve proposed a new workflow for existing action officers, the HSD personnel trained to respond to GearFit submissions. We’re currently testing this with one MAJCOM before iterating and scaling it. We’ve also expanded GearFit to include “collaborators,” subject matter experts who can support action officers when needed.
Through our research with female pilots, we learned that sharing knowledge and creating resources around equipment can help alleviate problems with information gaps. To this end, we built GearWiki, a platform that centralizes information about gear. We also updated GearFit’s marketing and communications to further drive adoption and empower more aircrew to submit feedback. These resources include guidance around submitting quality feedback, with the aim to provide better, more actionable data to decision-makers.
With GearFit’s foundation in place and the initial steps to scale it underway, we’ve begun to see the platform’s data translated into actionable requirements and changes. To expand GearFit’s impact, the team will continue to build out GearFit functionality, drive adoption, provide stakeholders the data they need, and develop operational solutions for long-term success.
The results
- Delivered an alpha version of the gear-fitment-feedback application within three months
- Drove initial aircrew adoption of the application, despite cultural and behavioral obstacles, through a marketing and communications campaign
- Demoed work to, and received praise from, former Secretary of the Air Force, Barbara Barrett, and her Chief of Staff, General David Goldfein
- Increased submission count by 1000% by switching to an easier authentication system
- Created buy-in across eight other MAJCOMs
- Became official feedback tool for an in-development bladder relief device
- Identified training gaps at units based on submissions indicating problems that could be solved at lower levels
- Identified an issue with a particular harness that cannot accommodate certain chest sizes, a short term solution is in place and longer term requirement as well
- Provided data to validate more than eight gear changes in flight
- Provided a space for ideas to be shared, resulting in the USAF’s consideration of a submitted idea for a survival kit improvement
- Garnered interest at a variety of events to expand GearFit to other career fields, such as AF security forces, DoD branches, and even other governments seeking solutions for gear in their communities